Autoindustrie vor neuer Ära: Sind die Tage des Fließbands gezählt?
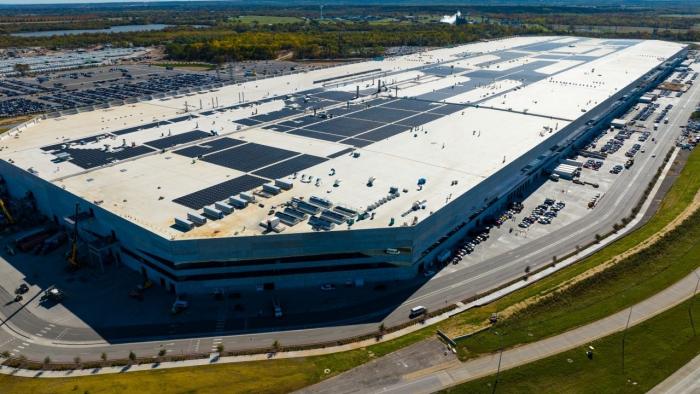
Tesla Gigafactory in Austin, Texas. Bild: Shutterstock.com
E-Autos: Kulturschock für die europäische Konkurrenz? Tesla probiert "unboxed"-Produktionssystem; Innovation im Konkurrenzkampf mit China.
Nicht nur bei den Fahrzeugen beschreitet Tesla neue Wege, auch bei deren Herstellung versucht Tesla mit etablierten Branchentraditionen zu brechen.
Mit dem derzeit in Austin (Texas) getesteten Unboxed-Produktionsverfahren geht es dem Fließband an den Kragen, jenem über einhundert Jahre alten Prinzips in der Fahrzeugmontage, bei dem zuerst die Karosserie montiert und dann nacheinander sämtliche weiteren Komponenten hinzugefügt werden.
Henry Fords Fließband
1913 ging es in Detroit bei Ford los mit der beweglichen Fertigung am Fließband, in der die Karosserie nacheinander Stationen durchläuft. So gelang es Ford, die Produktionszeit für das Modell T von 12 Stunden auf 93 Minuten zu senken.
Bereits acht Jahre später waren über die Hälfte aller Autos auf der Welt Modell Ts. Ford bot zu der Zeit auch nur eine Modellvariante an, das Modell T in Schwarz. Auch deshalb war Ford der Konkurrenz aus Deutschland haushoch überlegen.
Daimler bot im selben Jahr 57 verschiedenen Modellvarianten an, und war schon deshalb nicht in der Lage, auf Fords neue Produktionsweise umzusteigen. Dazu kam noch eine kulturelle Ablehnung, alles Amerikanische war den deutschen Autobauern suspekt.
Erst nach dem Krieg übernahmen auch die Deutschen Fords Methoden.
Bis heute kaum verändert
Seit über einhundert Jahren ist Henry Fords Innovation kaum verändert Rückgrat der Fahrzeugmontage. Das Verfahren hat jedoch auch Nachteile. Gleich zu Beginn wird die gesamte Karosserie zusammengebaut, ab dann wird am Fließband immer die "große Box" bewegt, obwohl nur punktuell daran gearbeitet wird, was viel Platz braucht.
Auch kann immer nur an wenigen Stellen gleichzeitig gearbeitet werden. Auch müssen sämtliche Komponenten durch die Öffnungen der Karosserie hindurch gefädelt werden, um an ihrem Platz montiert werden zu können.
Daher werden mitunter die Türen nach dem Lackieren wieder ausgebaut, um besser im Innenraum arbeiten zu können, um dann zu einem späteren Zeitpunkt erneut eingebaut zu werden.
E-Auto ermöglicht Produktionsinnovationen
Tesla stellt dieses Prinzip nun infrage. Anstelle einer großen Karosseriebox, der sich entlang eines linearen Förderbands bewegt, werden zunächst größere Teile (Vor- und Hinterteil, Seitenteile, Unterboden) getrennt belassen.
Die Folge sind mehrere Unter-Produktionslinien, an denen gleichzeitig an großen Teilen gearbeitet werden kann. Vor gut einem Jahr stellte der Vizepräsident für Fahrzeugtechnik bei Tesla Lars Moravy das neue "unboxed"-System erstmals am Tesla-Investorentag vor.
Derzeit wird im Tesla-Werk in Austin (Texas) an der Umsetzung gearbeitet. Neu ist die Methode allerdings nur für die Autoindustrie. In der Flugzeugindustrie kommen allein seit Jahrzehnten eine ähnliche Methode zum Einsatz – allein schon wegen der Größe der Flugzeuge.
Die Architektur von E-Autos – eine große Batterie im Unterboden und viel weniger Aggregate –ermöglicht nicht nur die Neukonzeption der Fahrzeuge selbst, sondern auch ihres Herstellungsprozesses. Der elektrische Antrieb kann so zu Produkt- und Produktionsinnovationen erleichtern, wenn die E-Autos von Grund auf neu konzipiert werden.
Das hat Tesla schon mit dem Gigacasting unter Beweis gestellt. Dabei handelt es sich um den Einsatz sehr großer Gussmaschinen, mit denen große Teile einer Fahrzeugkarosserie in einem einzigen Stück hergestellt werden können.
Der gesamte hintere und vordere Teil der Karosserie entsteht in einem Arbeitsgang, anstatt wie herkömmlich aus vielen Dutzend Blechteilen zusammengeschweißt zu werden.
Teslas Strategie
Hintergrund der neuerlichen Produktionsinnovation liegt in Teslas langfristiger Strategie. Bislang ging noch jeder Modellwechsel bei Tesla mit Skalierung hin zu größeren Stückzahlen und günstigeren Preisen einher.
Und mit jedem neuen Modell unterzieht Tesla auch die Produktionsverfahren einer gründlichen Revision. So geht jeder Modellwechsel mit einer umfassenden Veränderung der Produktionsmethoden einher. Für 2026 ist die nächste Skalierungsstufe geplant, der günstige Einstiegstesla für etwa 25.000 US-Dollar.
Entgegen Teslas Image als Hersteller teurer E-Autos, ist es Tesla langfristiges Ziel schon immer gewesen, günstige E-Autos in großen Stückzahlen zu produzieren. Tesla hat seine Zulieferer über Pläne informiert, mit der Produktion eines neuen Massenmarkt-Elektrofahrzeugs mit dem Codenamen "Redwood" zu beginnen.
Dieses Fahrzeug soll dann die Tesla-Architektur der nächsten Generation, intern als "NV9X" bekannt, im Unboxed-Verfahren zum Einsatz kommen. Um nochmals größere Stückzahlen und niedrigere Preise zu ermöglichen, sind Produktivitätssteigerungen nötig.
Autoexperte Bratzel, Leiter das Center of Automotive Management, hält das für entscheidend für den Durchbruch von E-Autos. Es gelte, "die Kosten von Elektrofahrzeugen entlang der Wertschöpfungskette weiter zu reduzieren und – gegebenenfalls durch Kooperationen – Skaleneffekte im Bereich Batteriezelle, Packaging sowie Design und Produktion der Fahrzeuge zu erzielen".
Teslas Konkurrenz ist längst nicht mehr die – im E-Sektor abgehängte deutsche und US-amerikanische Industrie, sondern die Konkurrenz aus China. Um gegenüber dieser Konkurrenz zu bestehen, beschreitet Tesla auch beim Produktionsprozess den Weg ständiger Prozessinnovationen.
Durch das Unboxed-Verfahren erhofft sich Tesla, diese Rationalisierungseffekte – wie schon beim Gigacasting – erzielen zu können. Das Beratungsunternehmen Caresoft aus Detroit hat ausgerechnet, dass eine solche Fabrik bis zu 30 Prozent weniger Platz und 40 Prozent weniger Personal benötige.
Es bleibt abzuwarten, ob Tesla ein weiteres Mal versuchen wird, den Endmontageprozess stärker zu automatisieren und im zweiten Anlauf durch Unboxing eine hochautomatisierte Fabrik zum Laufen zu bringen. Beim Model 3 war Tesla damit gescheitert, hatte zu viel automatisiert und bekam die Fertigung nicht in den Griff.
Warum gerade Tesla?
Warum ist gerade Tesla so innovativ, nicht nur beim E-Antriebe und Digitalfunktionen, an allen Ecken und Enden wird munter drauflos experimentiert?
Hier kommt Tesla seine Wurzeln als Tech-Startup aus dem Silicon Valley zugute, das auf Branchentraditionen und Zuliefernetzwerke pfeift.
Bei Tesla gilt kein "Das haben wir immer schon so gemacht", sondern die "first principles": Die Gesetze der Physik gelten, alles andere sind nur Empfehlungen.
Demgegenüber herrscht in der altehrwürdigen Industrie ein technologischer Konservatismus, eine Angst, bewährte Pfade zu verlassen. Oft sind es Innovationen, die die Etablierten selbst in ihren Forschungs- und Entwicklungsabteilungen zur Produktreife gebracht haben, die dann vom Management abgewürgt werden.
Ähnlich wie bei anderen Innovationen werden die etablierten Hersteller, wie schon beim Gigacasting absehbar, letztlich gezwungen sein, nachzuziehen, wie das schon bei vielen anderen Innovationen der Fall war.
Tesla versucht mit der neuerlichen Prozessinnovation seine Technologieführerschaft nicht nur bei der Fahrzeugtechnik, sondern auch bei der Herstellung zu behaupten. Und so eine ähnliche Rolle einzunehmen, wie sie vor einhundert Jahren Ford besetzt hat: die elektrische Massenmotorisierung anzuführen.